Products+
Latest Products
Contact Us
- Henan Bingo Pipeline Co., Ltd.
- Mobile: +86 15515596408(WhatsApp)
- Email: sales@bingopipes.com
- Tel: +86 371 8618 0298
- Add: R102, No. 123 Zhongyuan Middle Road, Zhongyuan District, Zhengzhou City, Henan Province, China
HDPE Pipes for Marine
HDPE pipe has many beneficial characteristics, such as light weight, flexibility, excellent bendability and wear resistance, which is very suitable for marine applications.
- 1.Delivery: 10-30 days depending on the total quantity.
- 2.Packing: 11.8m/ Pcs for 40ft or 5.8m/ Pcs.
- 3.CO (Certificate of Origin): China, CO could be provided by free.
- 4.Products Inspection: Raw material, production process, delivery or third-party factory inspection.
- 5.MOQ: Trial Order or 1*20ft containers by mixed loading.
Quick Details of High Density Polyethylene (HDPE) Marine Pipes and Fittings
Products details information | |
Product name | High Density Polyethylene (HDPE) Marine Pipes and Fittings |
Brand | Bingo pipeline(Customer brand is available) |
Dia Ranges | DN110-2000mm(4 inch-80 inch) |
Raw material | PE100, PE80, PE4710, PE3608, PE100RC... |
Application | Intake and outfall systems, water pre-treatment and desalination... |
Color | Black with blue stripes, black or others colors |
Standards | ISO 4427, EN12201, AS/NZS4130, ASTM 3035, DIN8074, GOST18599, ASTM F714, ISO8779... |
Matching products | HDPE pipe fittings, Customized PE fittings, floaters, Rubber hose, DI/ Steel backing ring flanges, dredging mud pump, welding machines and tools, etc. |
Company/Factory Strength | |
Production Capacity | 120*40ft containers/month |
Sample | Free sample could be provided |
Quality | QA & QC system, Ensure traceability of each process |
Warranty | 50 years with normal use |
Certificates | ISO9001, OHSAS 18001, ISO14001,CE... |
Delivery time | 5-30 days, depending on the quantity |
Test/Inspection | National Standard Laboratory/ Pre-delivery inspection |
Service | Research, Design, manufacture, Test, Sales, Solution Providing, After-sale service |
Management | Effective 8S Management System |
No. of employees | More than 300 people |
Welcome customers to visit the factory, or third party factory inspection is acceptable.
Description of High Density Polyethylene (HDPE) Marine Pipes and Fittings
Since the 1960s, solid-walled HDPE pipes have been used in marine applications in Europe. Over the years, the size of solid-wall PE marine pipes has been steadily increasing, the diameter could reach to 3000mm, PE pipe is the best choice for marine pipe to installation.
Several factors are crucial for the optimum choice of marine HDPE pipes, which include: pipe SDR, type of HDPE raw material, ballast blocks setup and internal pressure.
HDPE piping systems are the best choice for many applications on- and offshore. They are nontoxic and are approved for potable water transport. Thanks to their high fatigue strength, HDPE pipes and pipe strings that are installed offshore can be lowered to the seabed in a fast and safe manner. Since HDPE is also noncorrosive and there are no welding beads inside the continuously extruded pipeline, it is ready for long-term operation with a low-head loss, saving energy. Together with its high abrasion resistance and resilience to shocks, polyethylene is a much better solution than steel, GRP, or concrete piping for many applications.
Our long experience with pipeline design and deployment has led to very cost-effective fabrication and deployment methods. The polyethylene pipeline could be fused into long sections onshore where labor costs are lower, filled with air, then the assembled floating pipe is towed into place and lowered to the seabed often in a single day, minimizing expensive marine construction and weather-related risks.
Advantages of High Density Polyethylene (HDPE) Marine Pipes and Fittings
PE pipes are the best choice for marine installations. Basically, there are two types of production techniques: solid wall and helicoidally welded (structured pipes).
Abrasion resistance
PE pipes have better abrasion resistance than most other pipe material and PE pipes are often used for slurry pipelines in the mining industry. The abrasion in the pipe is dependent on the size, shape and concentration of the solids in the slurry as well as the angle of impact and the flow characteristics.
Chemical resistance
PE pipes are resistant to most chemicals, salts, acids and alkalis. However, petroleum products could cause a slight swelling of the PE material. Wetting agents and strong oxidizing liquids will impair the stress cracking resistance of PE and shorten the lifetime of the pipes. Information on the extent to which different chemicals may affect the lifetime of PE pipes can be found in chemical resistance tables published by various PE resin manufacturers and plastic pipe organizations.
Light weight.
Because HDPE pipes are in the “featherweight” class compared to steel or concrete pipes, and with a density of only 0.95 kg / dm³, it is able to float in the water without assistance. It is easy to transport and install.
Cost savings and higher operational reliability
For onshore job sites, we could delivery the shorter pipe length via truck, train or bulk shipment virtually everywhere. These pipes could be connected by butt fusion or flanges connection(the stub ends and backing rings on both ends could be pre-welded before delviery, the welding service could be provided by us), which could reduce the welding working for customer on at the job site and can be quickly joined with flange connections, resulting in shortened installation time and a range of cost saving. We had build up a reputation of delivering complete system solutions based on more than 10 years of application engineer worldwide.
Proven leak-tight fittings
Bingo pipeline is a one stop supplier, supplying the complete range of fittings, for customers pipes system in the highest quality resins and certified according to the ISO9001 Quality Management System. The fittings including the butt fusion fittings, customized fabricated fittings by the pipes, and some unconventional fittings. These fittings are essential components in any piping system, serving the connect straight pipes, to adapt pipes to different sizes or shapes, and to regulate the flow of the contents. Bingo Pipeline is a pioneer in PE pipes and fittings production, and we had built upon profound technical expertise that encompasses the complete installation process. A huge range of large diameter fittings for butt fusion or electro fusion welding fittings are available. We provide the stub ends flanges, reducer, bends, Tee, intake heads, which could be together with the pipes, more stronger and have good Leakage and wear resistance.
Specifications of High Density Polyethylene (HDPE) Marine Pipes and Fittings
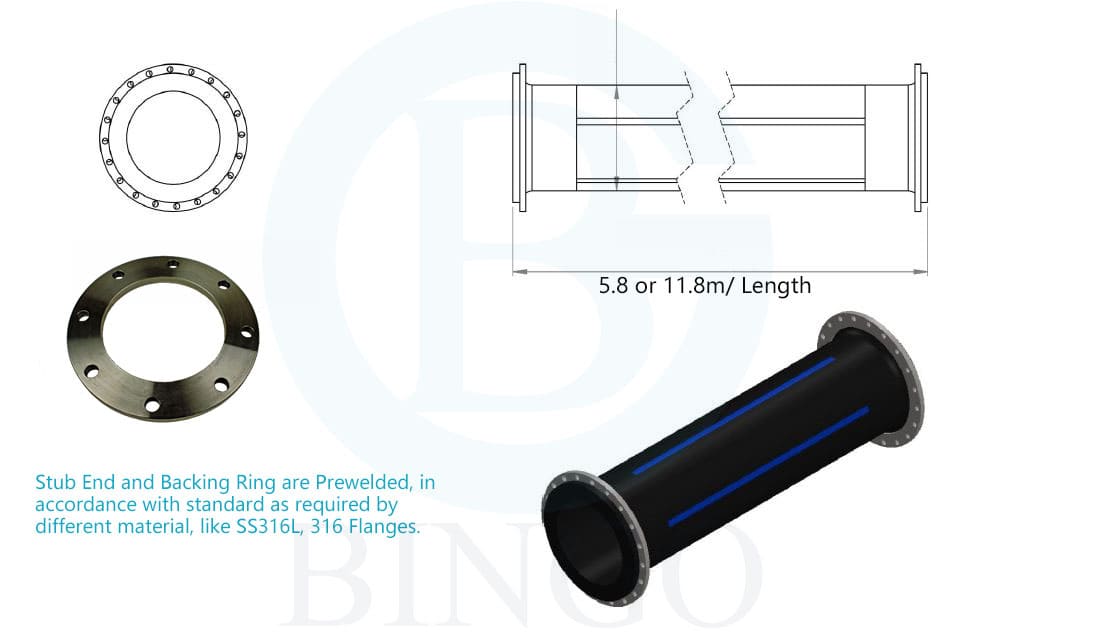
Wall thickness minimum and maximum values are obtained from EN 12201-2:2011+A1:2013 | |||||||||
Maximum and minimum wall thicknesses | |||||||||
HDPE pipe series | |||||||||
PE100 | SD21 | SDR26 | SDR33 | ||||||
Norminal Diameter DN (mm) | Norminal Pressure, PN in bar | ||||||||
PN8 | PN6 | PN5 | |||||||
Wall Thickness (mm)& Weight | |||||||||
emin | emax | Weight (kg/m) | emin | emax | Weight (kg/m) | emin | emax | Weight (kg/m) | |
355 | 16.9 | 18.7 | 18.63 | 13.6 | 15.4 | 14.83 | 10.9 | 12.1 | 12.00 |
400 | 19.1 | 21.2 | 23.69 | 15.3 | 17 | 18.80 | 12.3 | 13.7 | 15.27 |
450 | 21.5 | 23.8 | 29.88 | 17.2 | 19.1 | 24.27 | 13.8 | 15.3 | 19.22 |
500 | 23.9 | 26.4 | 36.79 | 19.1 | 21.2 | 29.93 | 15.3 | 17 | 23.70 |
560 | 26.7 | 29.5 | 42.48 | 21.4 | 23.7 | 34.38 | 17.2 | 19.1 | 27.85 |
630 | 30 | 33.1 | 58.47 | 24.1 | 26.7 | 47.57 | 19.3 | 21.4 | 38.49 |
710 | 33.9 | 37.4 | 68.37 | 27.2 | 30.1 | 55.40 | 21.8 | 24.1 | 44.75 |
800 | 38.1 | 42.1 | 94.32 | 30.6 | 33.8 | 76.54 | 24.5 | 27.1 | 61.87 |
900 | 42.9 | 47.3 | 109.68 | 34.3 | 38.3 | 88.58 | 27.6 | 30.5 | 71.83 |
1000 | 47.7 | 52.6 | 147.44 | 38.2 | 42.2 | 119.73 | 30.6 | 33.5 | 96.49 |
1200 | 57.2 | 63.1 | 212.02 | 45.9 | 50.6 | 172.04 | 36.7 | 47.3 | 138.77 |
1400 | 66.7 | 73.5 | 265.28 | 53.5 | 59 | 214.89 | 42.9 | 47.3 | 173.67 |
1600 | 76.2 | 84 | 346.37 | 62.1 | 67.5 | 284.89 | 49 | 54 | 226.71 |
1800 | 85.7 | 94.5 | 438.25 | 69.1 | 75.8 | 356.78 | 54.5 | 60.8 | 283.77 |
2000 | 95.2 | 105 | 540.93 | 76.9 | 84.2 | 441.15 | 60.6 | 67.5 | 350.58 |
Other specifications have not been shown on our dimension chart, please CONTACT US for more information
Application of High Density Polyethylene (HDPE) Marine Pipes and Fittings
Since the early 1960’s, just a few years after its first introduction, polyethylene (PE) piping has been increasingly used for various marine applications such as effluent outfalls, river and lake crossings, and fresh and salt-water intakes. Immunity to galvanic corrosion is a major reason for selecting PE. The combination of air and water, but particularly seawater, can be very corrosive to ordinary metallic piping materials. But many beneficial features, combine to make PE piping particularly well-suited for marine applications:
The HDPE pipelines are suited for:
- Seawater air conditioning (SWAC)
- Ocean thermal energy conversion (OTEC)
- Marine outfalls
- Aquaculture and mariculture
- Industrial cooling and power:
- Waste heat power cycles
- Power plant cooling
- Liquefied natural gas (LNG) process cooling
- Chemical process cooling
- Other industrial processes with large cooling loads
- Intake and outfall pipeline from 6" Diameter to 144" Diameter, both inshore and offshore
- Bridge and pier construction and rehabilitation
- Power plant projects
- Intake and discharge pipeline construction for cooling water systems
- Penetration, inspection and cleaning of pipelines and approach tunnels
- Remedial installation of zebra mussel protection systems
![]() |
![]() |
HDPE Pipes for Wastewater Disposal | HDPE Pipes for Submarine |
![]() |
![]() |
HDPE Pipes for Ocean Cleanup Project | HDPE Pipes for Dredging |
High Density Polyethylene (HDPE) Marine Pipes and Fittings
Write Down Your Question
We are not only a product manufacturer, also a solution provider, whether you have a Question or Request For Quotations, we're here to help.